What: 📅 Lean Summit 2024
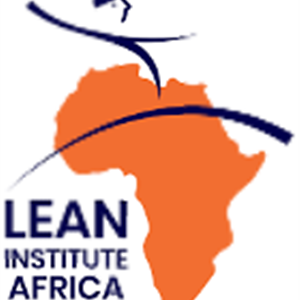
https://www.quicket.co.za/events/275454-lean-summit-2024/
When:
Where: 🕳 UCT Graduate School of Business
How much:
🎟️ R1995.00Quicket
🎟️ R2995.00Quicket
🎟️ R3995.00Quicket
Join us at the LIA Summit!
Industry leaders and practitioners will discuss the latest trends, challenges, and opportunities in Lean management. Engage in insightful discussions, network with industry peers, and gain practical knowledge to advance your Lean journey. Themes:Developing and Engaging Your PeopleStaying Current in the Evolving Digital AgeBest-Practice Industry Training Practices Keynote Speakers: Mike Hoseus (USA)Co-author of Toyota Culture: The Heart and Soul of the Toyota WayKeynote: Integrating Digitalization and Lean in a High- Performance Culture John Vellema (Denmark)Co-author of Building a Global Learning Organization: Using TWI to Succeed with Strategic Workforce Expansion in the LEGO GroupKeynote: Case Studies on TWI Implementation, from global multinationals to local businesses Jake Morris, BMA (South Africa)COO of BMA (Benchmarking and Manufacturing Analysts)Why South Africa’s future depends on Lean manufacturing Terry O’Donoghue, Halfway Toyota (South Africa)Case Study on Lean Leadership Break-out Presenters:Ayesha Augustus, Western Cape Government (South Africa) - “Red Tape Reduction Unit” Case StudyDr. Greg Bellairs, Western Cape Blood Services (South Africa) - Implementing Continuous Improvement at a non-competitive, non-profit entity – why bother?Juane Schutte, Jendamark (South Africa) - Effective On-the-Job Training Strategies for Front-Line WorkersSean Mercer, BMA (South Africa) - Cape Union Mart factory’s 6-month profit turnaroundDr. Tony Booysen, Arwyp Medical Centre (South Africa) - The A3: Shared Learning from Shared Learning
Confirmed AgendaAll workshops and presentations will be held at the UCT Graduate School of Business. Tuesday, 26 November8:30am Full-Day WorkshopMike Hoseus - Toyota Culture6:00pm Speaker’s DinnerGINJA Restaurant, V&A Waterfront Wednesday, 27 November8:30am Welcome and IntroductionLean Institute Africa (Samantha Allen, Tshepo Thobejane, and Ben Hoseus)8:45am Keynote AddressMike Hoseus (USA) - Toyota Culture9:30am Keynote AddressJake Morris (South Africa)
- South Africa’s future depends on Lean manufacturing10:15am Break10:45am Break-out SessionsDr. Greg Bellairs, Western Cape Blood Services (South Africa) - Implementing Continuous Improvement at a non-competitive, non-profit entity – why bother?Ayesha Augustus, Western Cape Government (South Africa) - “Red Tape Reduction Unit” Case Study11:45am Lunch12:45pm Keynote AddressJohn Vellema (Denmark) - Building a Global Learning Organization: Using TWI to Succeed with Strategic Workforce Expansion in the LEGO Group1:30pm PresentationSean Mercer, BMA and Andy Thorvaldsen, Cape Union Mart (South Africa) - Cape Union Mart factory’s 6-month profit turnaround2:15pm Break-out SessionsDr. Tony Booysen, Arwyp Medical Centre (South Africa) - The A3: Shared Learning from Shared LearningJuane Schutte, Jendamark (South Africa) - Effective On-the-Job Training Strategies for Front-Line Workers3:15pm Break3:30pm Keynote AddressTerry O’Donoghue, Halfway Toyota (South Africa) - Lean Leadership Case Study4:15pm Closing AddressLean Institute Africa (Samantha Allen, Tshepo Thobejane, and Ben Hoseus) Thursday, 28 November8:30am Full-Day WorkshopJohn Vellema - Building a Global Learning Organization: Using TWI to Succeed with Strategic Workforce Expansion in the LEGO Group Workshop Details Tuesday, 26 November8:30am Full-Day Workshop with Mike Hoseus - Toyota Culture Workshop Overview:Join us for a transformative full-day workshop led by Mike Hoseus, co-author of Toyota Culture. You’ll delve into the core principles of building a high-performance organizational culture through dynamic sessions. The workshop will cover several key development models, including Mike’s 4P model—purpose, People, Process, and Problem-Solving. Participants will explore how these principles are integrated into Toyota’s culture to drive continuous improvement and exceptional performance. Learning Objectives: Purpose: Learn to develop and align your organization’s strategy with its mission, vision, and values. Understand True North (Hoshin) and how to apply servant leadership principles effectively.People: Discover best practices for employee engagement, hiring, and cultivating a Lean culture. Explore the Lean Management System and core competencies essential for sustained success.Process: Gain insights into Cross-Training, Just-In-Time (JIT) processes, Standardization, and optimizing Value Stream Performance.Problem-Solving: Understand A3 Thinking, the PDCA cycle, and the Toyota Business Practice (TBP) for effective leadership problem-solving and decision-making. What You’ll Receive: Eight hours of executive leadership workshop sessions led by Mike HoseusPrinted course materials, including exclusive references from Toyota CulturePre-workshop materials and personalized guidance directly from Mike HoseusYour Key Takeaway:You’ll leave the workshop with a tailored individual and organizational action plan designed to elevate your leadership capabilities and drive your organization’s development journey to the next level of performance. Participant Feedback: “I was thrilled to learn about the culture at Toyota and how servant leadership is applied in practice. It reinforced that the model is effective in any environment.““Mike’s presentation content was exactly what I needed. I gained numerous tools to implement Lean practices in our company.““I expected to learn to implement Lean but received so much more. Mike’s passion and clarity in teaching were truly inspiring.”
Take advantage of this opportunity to learn from a true expert and return proven leadership and Lean practices to your organization. Thursday, 28 November8:30am Full-Day Workshop with John Vellema - Building a Global Learning Organization: Using TWI to Succeed with Strategic Workforce Expansion in the LEGO Group Join us for an engaging workshop that provides foundational knowledge of TWI (Training Within Industry) and its role in enhancing your Lean initiatives. This powerful approach to training and workforce development boosts productivity. It fosters continuous improvement, making it ideal for managers, team leaders, and quality, safety, and HR professionals seeking effective organizational training methodologies. You will leave this workshop with practical skills and strategies that can be immediately applied in your workplace. In this workshop, you will learn the essentials of the TWI J Programs and explore the Enabling Process—a tested implementation strategy based on global best practices. Many organizations realize they have focused too much on Lean tools without cultivating a Lean culture. TWI supervisor training is essential for sustainable Lean transformation, emphasizing that achieving primary process stability is the first step towards Standardized Work. The TWI J Programs teach supervisors how to instruct (Job Instruction), lead (Job Relations), and improve (Job Methods). Key highlights include an overview of TWI’s foundational principles, its history supporting Lean practices, and interactive activities demonstrating Job Instruction’s effectiveness. Participants will engage in hands-on exercises to experience training methods that enable individuals to learn new jobs quickly and accurately. Additionally, real-world applications will be discussed, showcasing how TWI J Programs streamline processes and resolve workplace challenges. Success stories will illustrate transformations achieved through TWI, and a Q&A throughout the workshop will allow attendees to share experiences and learn best practices for integrating TWI into their organization. By the end of the workshop, you will have a solid understanding of the TWI J Programs and how to leverage these methods to enhance your organization’s business through your people. Take advantage of this opportunity to elevate your Lean efforts!